製造業の工場や生産現場でよく耳にするのが、稼働率という言葉です。
稼働率を無理に高めようとすると、生産性が落ちたり余剰在庫を抱える恐れがあります。
この記事では稼働率が表す意味と可動率との違い、具体例を交えた計算方法を解説します。
製造業で理想的な稼働率もお伝えするので、生産効率を高めたい担当者の方は、ぜひ参考にしてみてください。
稼働率とは?
稼働率(英語:Operating ratio)とは稼働可能な時間に対して、どれほど稼動できたかという割合を示す指標のことです。
主に生産工場や設備、機械といった製造業で使われる用語です。
例えば1日100個作れる設備で80個作った場合の稼働率は80%、120個作った場合の稼働率は120%となります。
設備の稼働時間が長いほどその設備から生産される量が増えることから、生産の効率性を判断する重要な指標となるのです。
稼働率は需要・オーダーがあることが前提で、需要・オーダーが多ければ稼働率が100%を超えることもあります。
生産性指標「稼働率と可動率」の違い
稼働率は人がどれほど作業したか、設備がどれほど稼動したかを示す指標です。
可動率(べきどうりつ、英語:operational Availability)は設備が正常に稼働可能な時間に対して、正常に稼働した時間の割合を示す指標です。
可動率の計算式には、設備にトラブルが発生して停止した時間を除いた時間が用いられます。
稼働率と違い需要・オーダーの影響は受けず、可動率が100%を超えることはありません。
稼働率と可動率の違いを簡単にまとめると、次のようになります。
- 稼働率:生産効率を表す指標
- 可動率:運転効率を表す指標
稼働率と可動率は、生産性の向上が目的という部分においては共通です。
なお、稼働率の計算方法は「生産量ベース」と「稼動時間ベース」の2通りあります。
- 生産量ベース:稼動率(%) = 実際の生産量 ÷ 生産能力 ×100
- 稼動時間ベース:稼動率(%) 実際の稼動時間 ÷ 本来稼動すべき時間 × 100
可動率の計算式は以下の通りです。
- 可動率(%) 正常だった運転時間 ÷ 総運転時間 × 100
設備総合効率(OEE)とは?
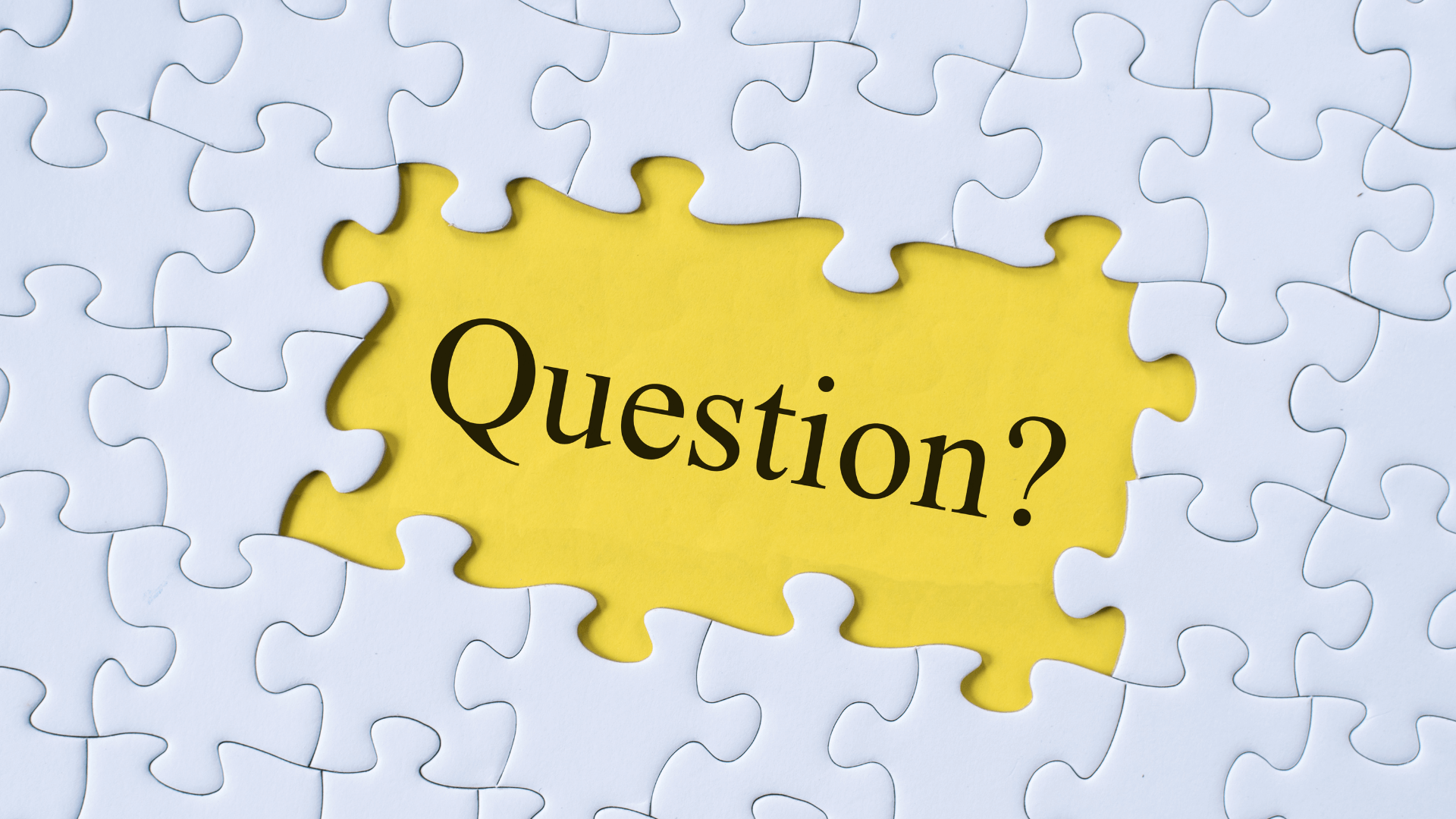
設備総合効率(英語:Overrall Equipment Effectieness)とは、自動化ラインを中心とした設備保全に関する指標の1つです。
公益社団法人日本プランドメンテナンス協会が提唱し、国際標準の規格として国内外の多くの企業で活用されています。
設備総合効率の計算式は以下の通りです。
- 設備総合効率 = 時間稼働率 × 性能稼働率 × 良品率
生産ラインのムダやロスといった要因を浮き彫りにして、改善に役立てることができます。
稼働率・可動率を計算するときに必要なデータと評価例
稼働率・可動率の計算に必要なデータや、計算・評価の方法を例を交えて紹介します。
稼動実績データ
稼働率を時間ベースで評価するには、設備ごとの稼動実績データが必要になります。
稼動実績データの項目例は、以下を参考にしてみてください。
- 設備名
- 稼動状況
- 開始時刻
- 終了時刻
基準時間データ
評価の基準時間は、実績データからは分かりません。
そのため、稼動日数や稼動可能時間をあらかじめ設定しておきましょう。
稼働率・可動率の計算と評価
以下のような事例を用いて、稼働率・可動率を計算してみます。
【稼動実績データ】
設備名 | 稼動状況 | 稼動状況の詳細 | 開始時間 | 終了時間 | 時間 |
レーザー溶接加工1号機 | 手動運転 | 8:30 | 12:00 | 3時間30分 | |
レーザー溶接加工1号機 | 昼休憩 | 12:00 | 13:00 | ||
レーザー溶接加工1号機 | 手動運転 | 13:00 | 15:00 | 2時間 | |
レーザー溶接加工1号機 | 異常停止 | 水温異常エラー | 15:00 | 16:00 | 1時間 |
レーザー溶接加工1号機 | 手動運転 | 16:00 | 17:30 | 1時間30分 | |
合計時間 | 8時間 | ||||
運転時間(実働) | 7時間 |
【基準時間データ】
設備名 | 1日あたりの基準時間 |
レーザー溶接加工1号機 | 7時間 |
【指標(計算結果)】
稼働率 | 可動率 |
114.28% | 0.875% |
ある日の稼動時間は昼休みを除くと8時間であり、稼働率は「8時間÷7時間」で約114%でした。
8時間のうち1時間は異常停止していたため、生産できた時間は7時間で可動率は「7時間÷8時間」で約88%になります。
稼動率が100%を超えており一見良さそうですが、実際はトラブルの影響で可動率が下がっています。
したがって、可動率の低さを補うために残業で稼動させたと推測評価ができるのです。
異常停止した原因は水温異常だったことから、防止策を検討したり異常時にすぐに対応できる体制を整えたりすることが重要になります。
製造業の理想の稼働率とは?
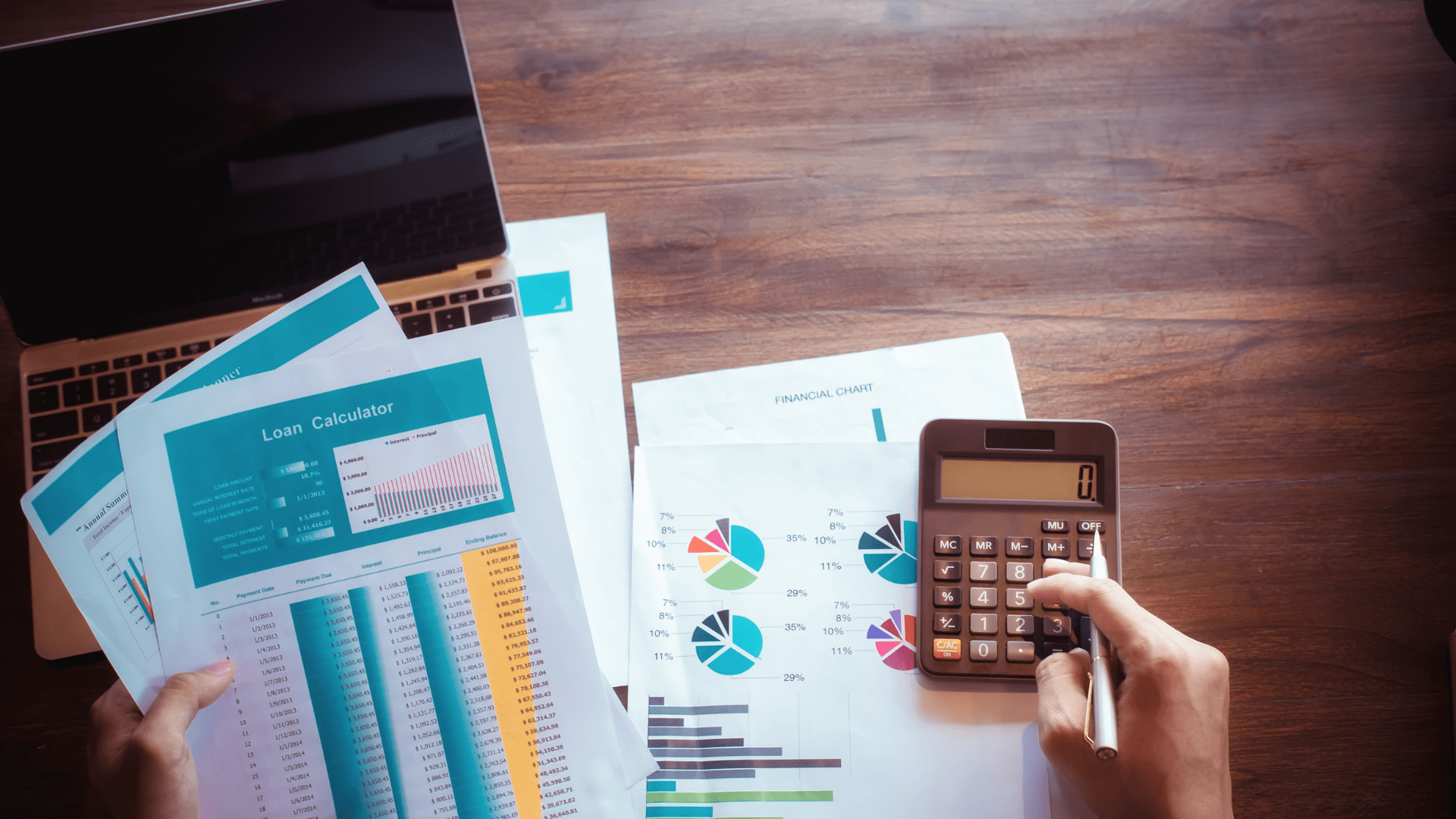
製造業の理想の稼働率を定義するならば「受注数と生産数のバランスが取れていて、稼働率が100%に近い状態」といえます。
改めて、稼働率の計算式を確認してみましょう。
- 生産量ベース:稼動率(%) = 実際の生産量 ÷ 生産能力 ×100
- 稼動時間ベース:稼動率(%) 実際の稼動時間 ÷ 本来稼動すべき時間 × 100
実際に現場の生産能力はさまざまな要因で変動するため、単純な計算では稼働率を求められないことも多いです。
生産能力をはるかに超える受注は、設備に過負荷を与えたり従業員の過労を招いたりする恐れがあります。
生産能力に対して受注が極端に少ない場合は設備の空転時間が増え、人材コストがかさむなど生産コストが無駄にかかることになります。
生産能力を最大限に活用しつつ、万が一のトラブルに対応できる可動率が重要なのです。
製造業の稼働率を上げる方法
稼働率を可視化する
工場の稼働率を上げるには、現在の稼働状況・業務状況を把握する必要があります。
稼働率を可視化する方法としておすすめなのが、工数管理ツールです。
工数管理ツールは「誰が」「何の業務に」「どれくらい」時間がかかったかを、把握するツールを意味します。
プロジェクト単位やタスク単位で稼働状況を可視化することで、ボトルネックを分析したり稼働率を改善したりできます。
計画を最適化する
稼働率は計画の最適化でも高めることが可能です。
一般的に、製造業では繁忙期と閑散期があります。
受注量に差がある場合は人員配置を適正化することで、コストを抑えながら稼働率を高められるのです。
また、プロジェクトによって必要な人員は異なるものです。
少人数でもプロジェクトを回せるのであれば、手持ち無沙汰になる人員が出ないように人員配置を変更するのも良いでしょう。
スキルアップの時間を設ける
従業員のスキルアップは中長期的にみて、稼働率を上げる方法として有効です。
例えば生産ラインに作業に慣れていない従業員が多いと、思うように生産量が得られないケースもあるでしょう。
業務経験の浅い従業員が研修やOJTでスキルアップできれば、一人当たりの生産量が増えて稼働率の向上につながります。
スキルアップの時間は一時的に生産量が減る可能性がありますが、少しでも早く取り組むことでリターンを得る機会を早めることが可能です。
稼働率を無理に高めてはいけない?
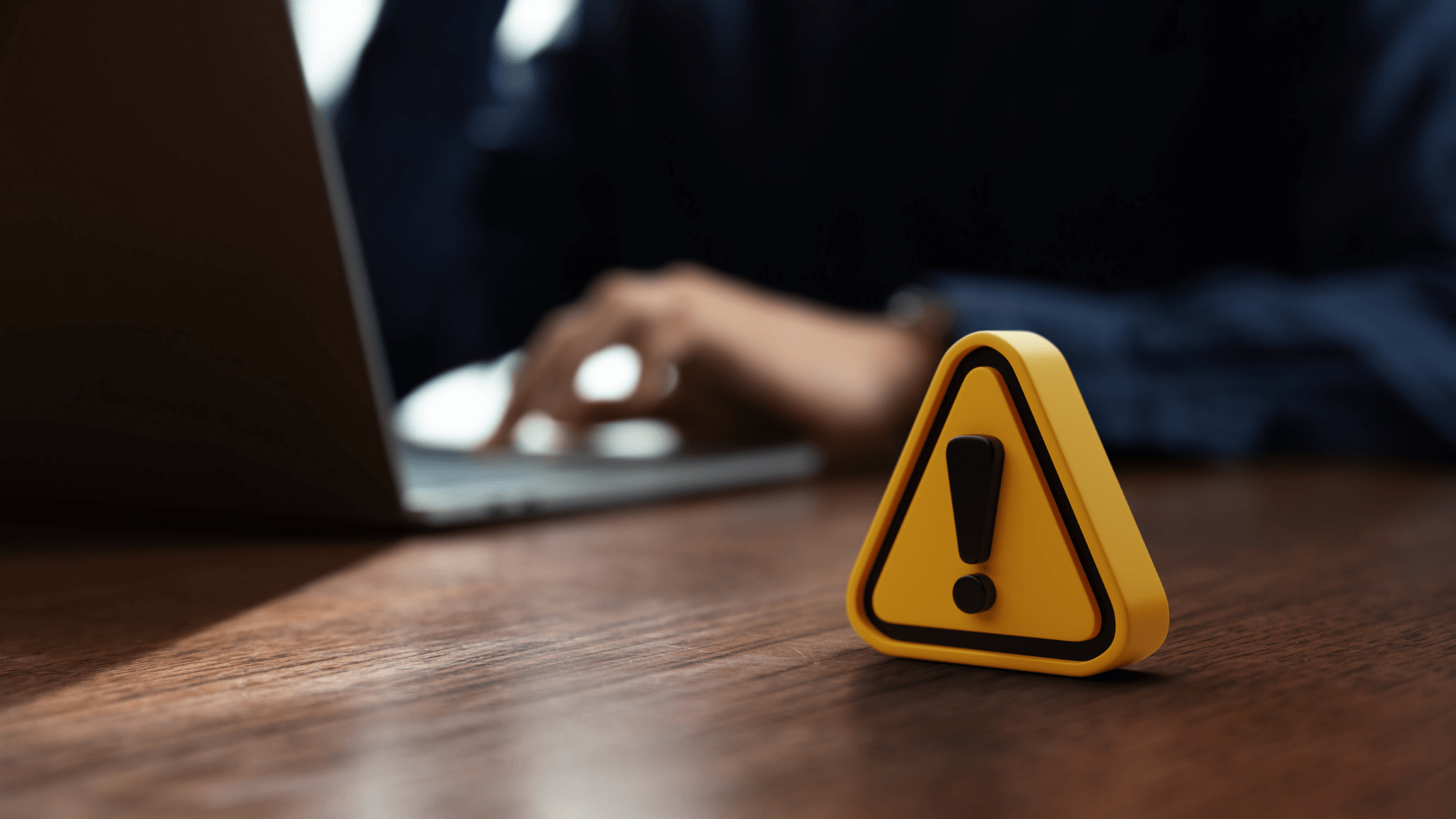
ここまで解説した通り生産現場の稼働率は、受注数と生産数のバランスが取れていて、トラブルにも対処できる稼働率が理想です。
稼働率を100%に近付けたい気持ちは理解できますが、無理に高めるのは良くありません。
例えば稼働率を高めるために、当初の生産計画以上に生産したとしましょう。
その結果、すぐに売れない在庫品が大量に倉庫に積み上がることになります。
売れるあてのない在庫品を大量に抱えてしまうと、企業の財務状況を悪化させる恐れがあるのです。
したがって、あまり数字に捉われすぎず、全体を見回しながら自社に適した稼働率を見極めることが重要になります。
まとめ:稼働率を無理に高めてはいけない理由とは?
ここまでお伝えした通り、稼働率は高ければ良いわけではありません。
状況によって適正な数値があり、無理に高めようとすると設備に過負荷を与えたり従業員の過労を招いたりします。
現場にムリやムダを発生させないためにも、まずは工数管理ツールを導入して現状把握から始めてみてください。